Promat Academy
In our daily lives, we encounter many printed materials; newspapers, magazines, brochures, and much more. Have you ever wondered what stages are involved in the creation process of these materials? Behind the scenes, there is a detailed and meticulous process where art and technology converge. Our printing house operates with a workflow that brings these printed works to life, emphasizing fine details and adhering to quality standards. We would like to introduce you more closely to the services offered by our printing house and this unique production process
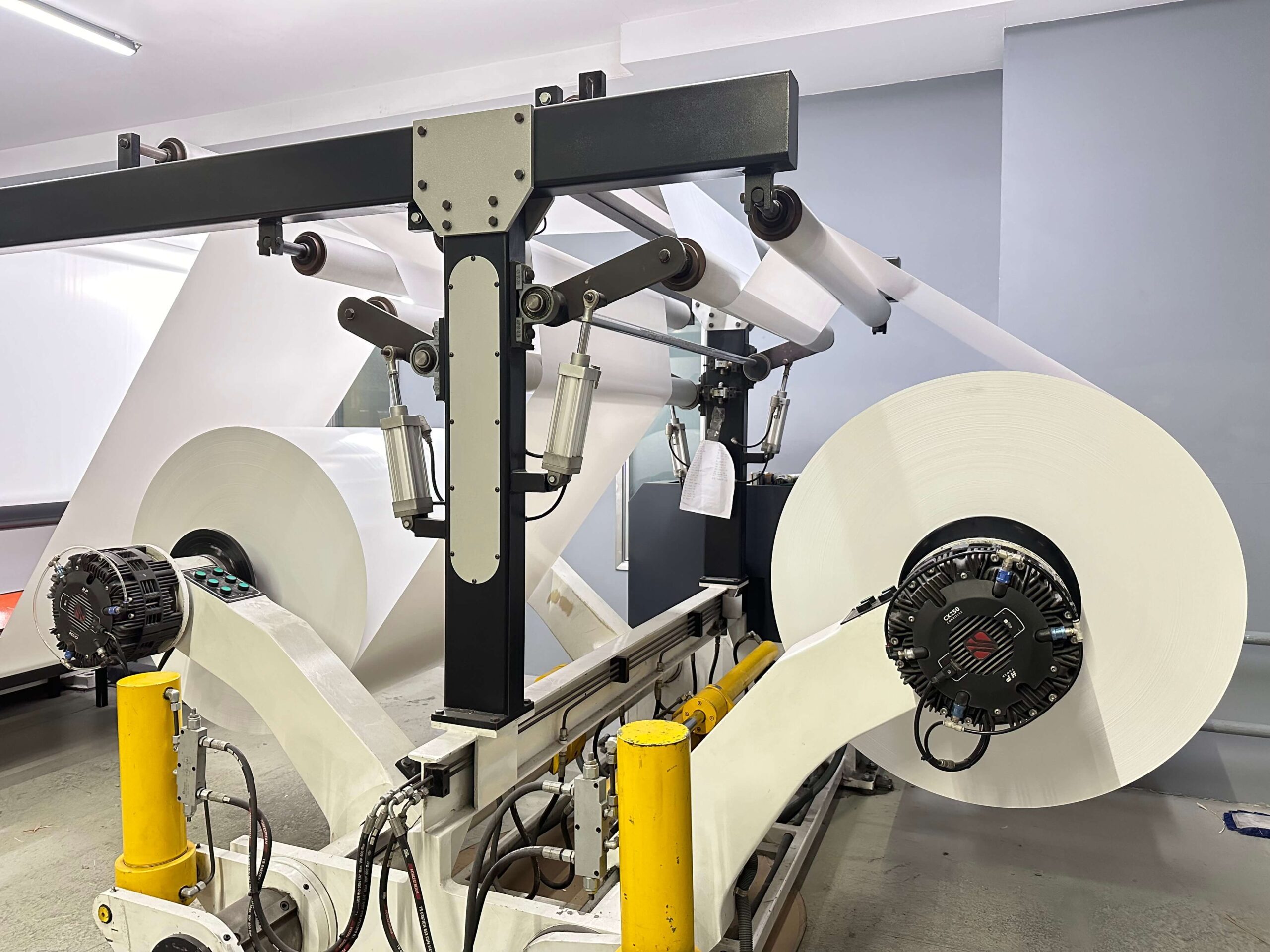
Pre-Printing
The preparation phase consists of film output/plate output, assembly phase, and plate phase.
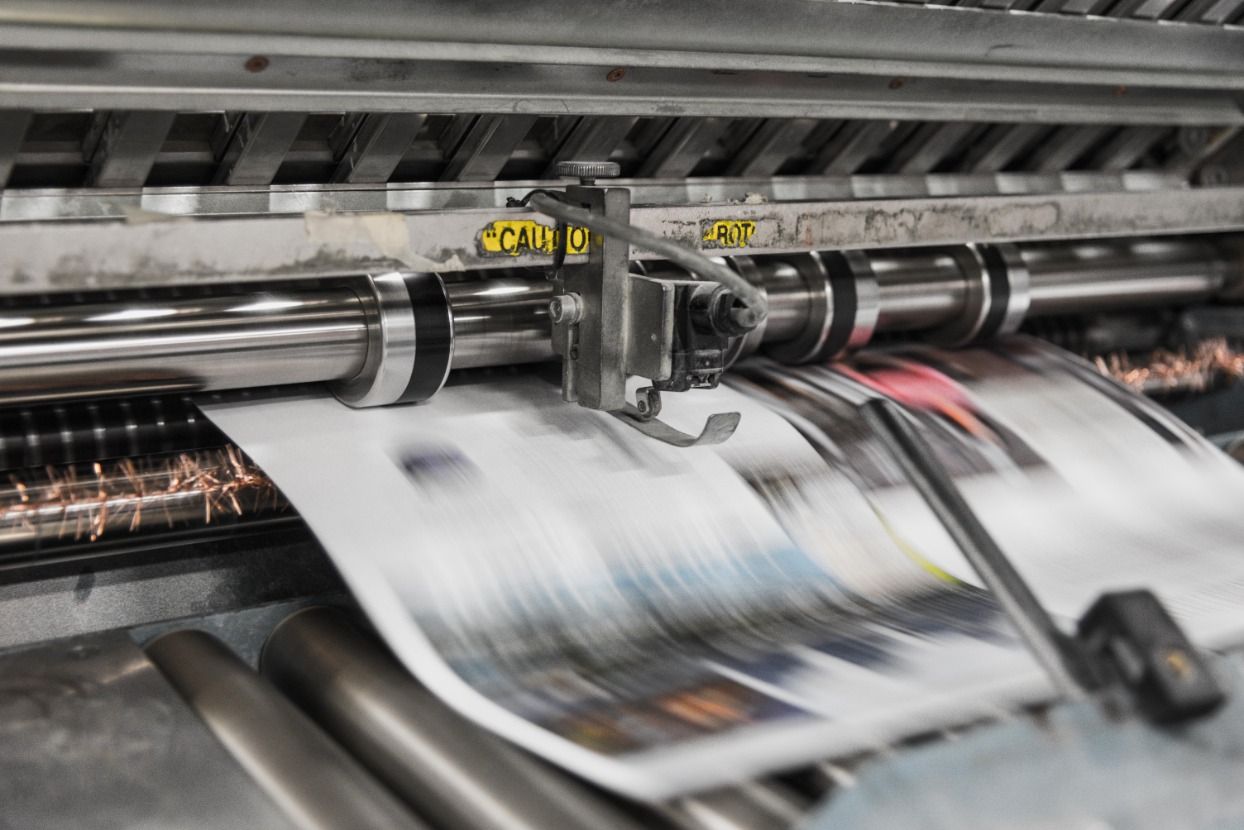
At the end of the pre-printing processes, the plate obtained is attached to the printing machine, transitioning to the printing phase. The printing plates are mounted on the machine, ink settings are adjusted, and then printing begins.
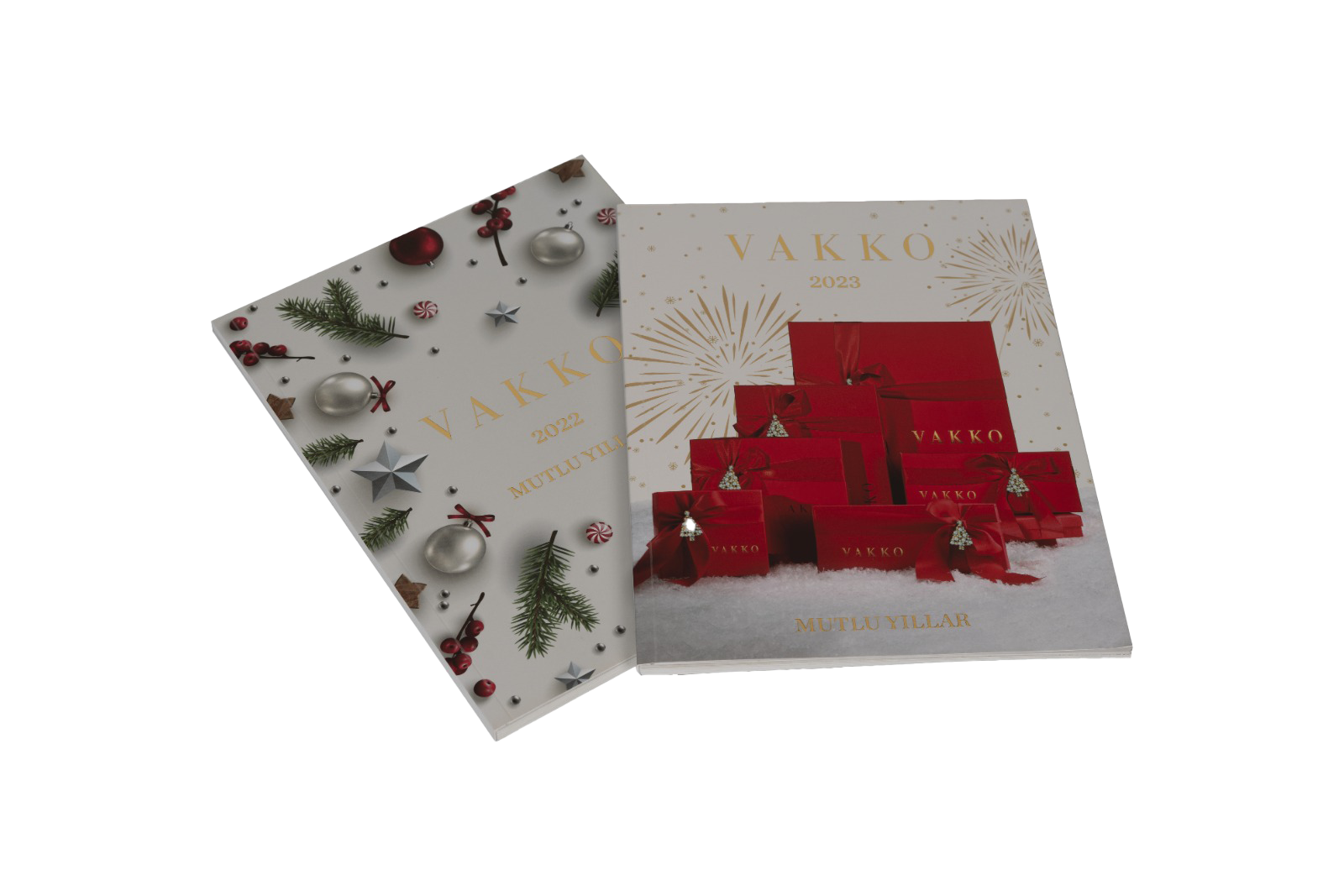
Post-Printing
After the printing is completed, the post-printing processes of the job begin. The stage of bringing the product into the form in which it will reach the final user takes place at this stage. In this phase, operations like binding, folding, collating, cover attachment, and wire stitching are carried out.
Characteristics of Papers According to Printing Systems
- Offset Printing Papers and Their Characteristics
- Gravure Printing Papers and Their Characteristics
- Letterpress Printing Papers and Their Characteristics
- Rotary Offset (Web Offset) Printing Papers and Their Characteristics
- Screen Printing Papers and Their Characteristics
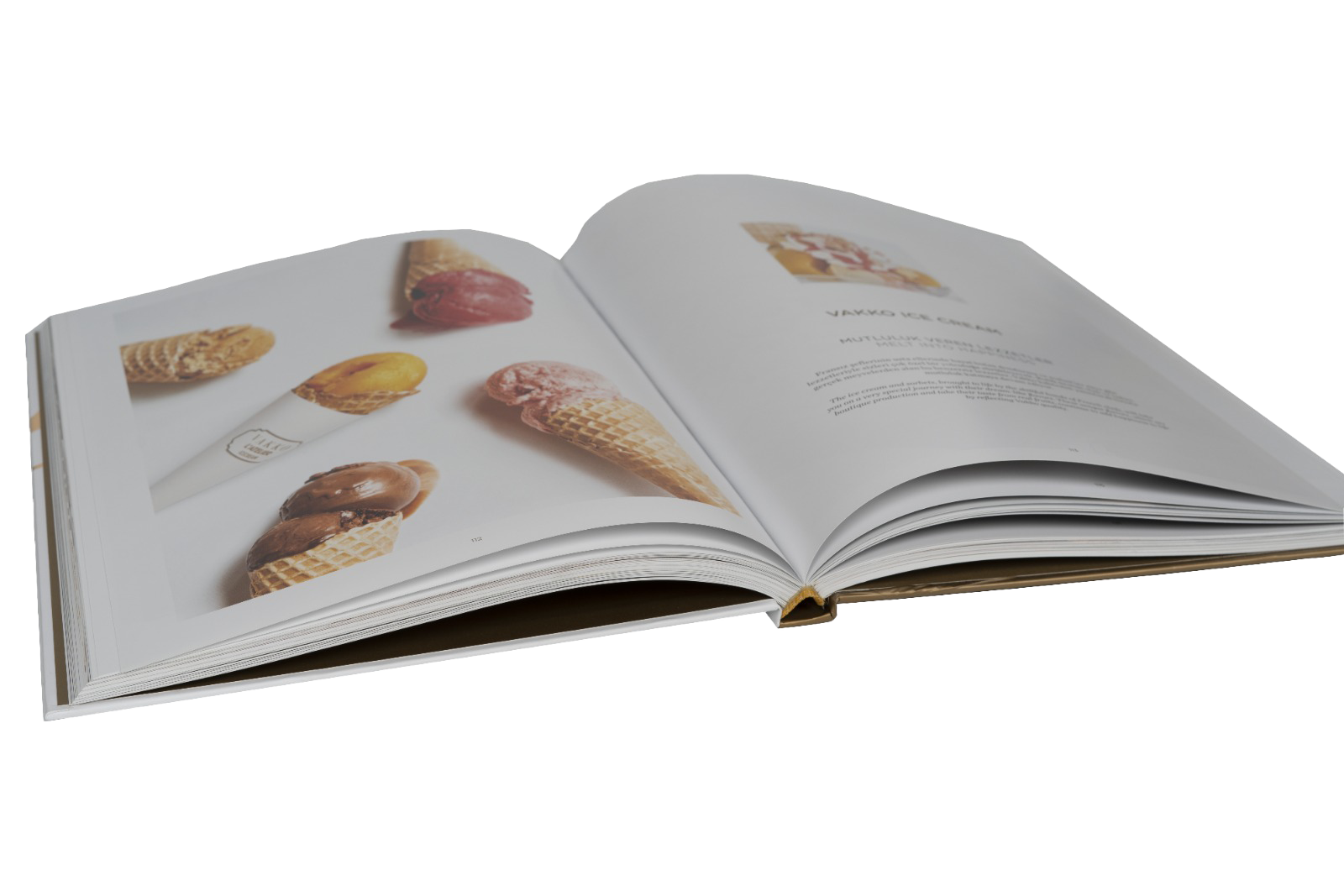
In this printing technique, it is not essential for the papers used to have a smooth and even surface for printing quality. Printing can be done on embossed and textured papers as well. In offset printing, the blanket that transfers the ink can easily transfer the ink to the rough and porous parts of the paper. This makes it possible to print fine halftones. However, it is easier to print on flat, smooth, and uniformly thick papers in offset printing.
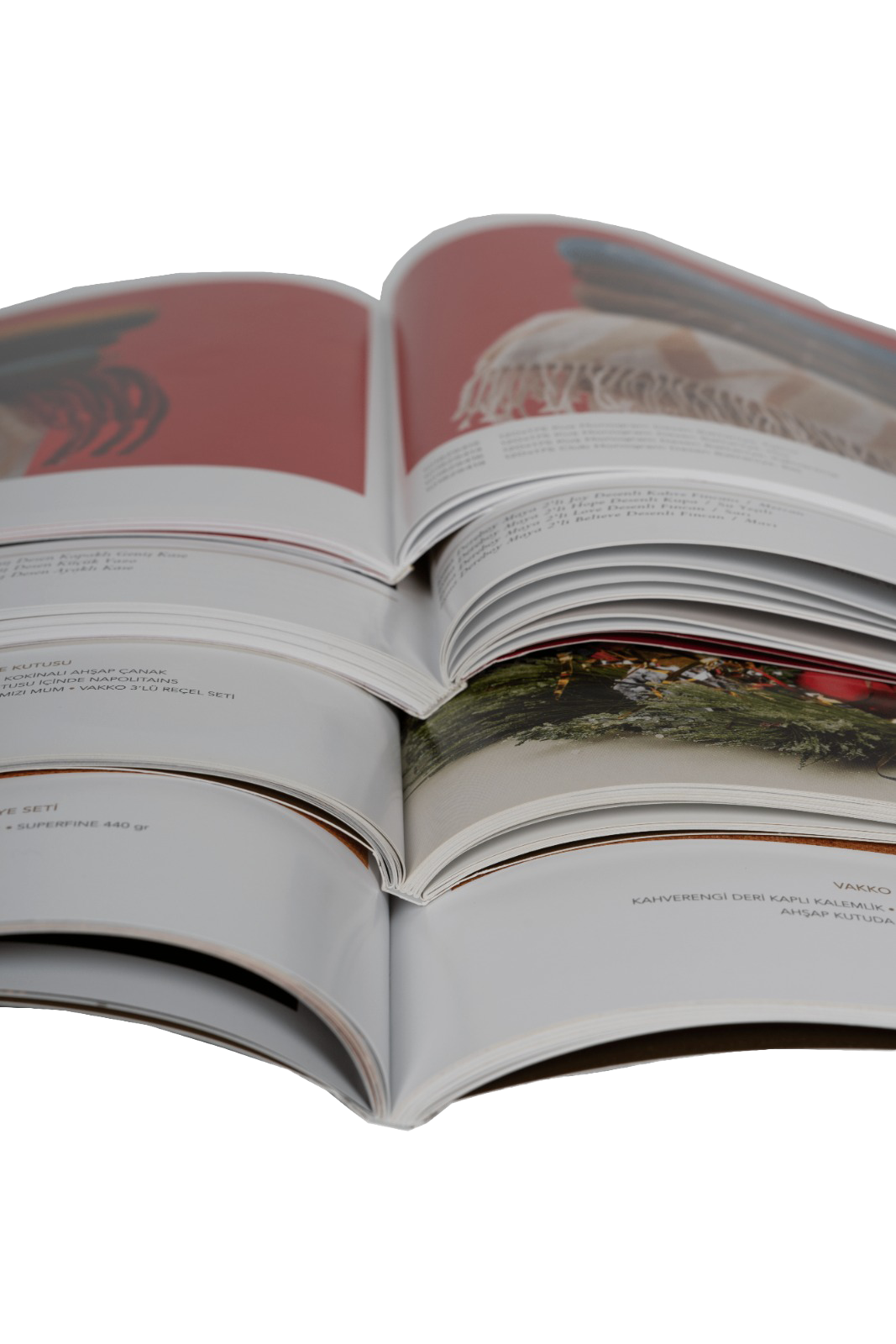
Gravure printing papers should be of uniform thickness, soft, and elastic to ensure compatibility with the cylindrical gravure printing plate. In this type of printing, the ink used is fluid, so the absorbency of the paper during drying is very important. The paper needs to be absorbent, which means it should be lightly glued. As in rotary printing, the winding of the reel is also very important in this method. If the characteristics of the paper are as desired, the matte and glossiness become less critical.
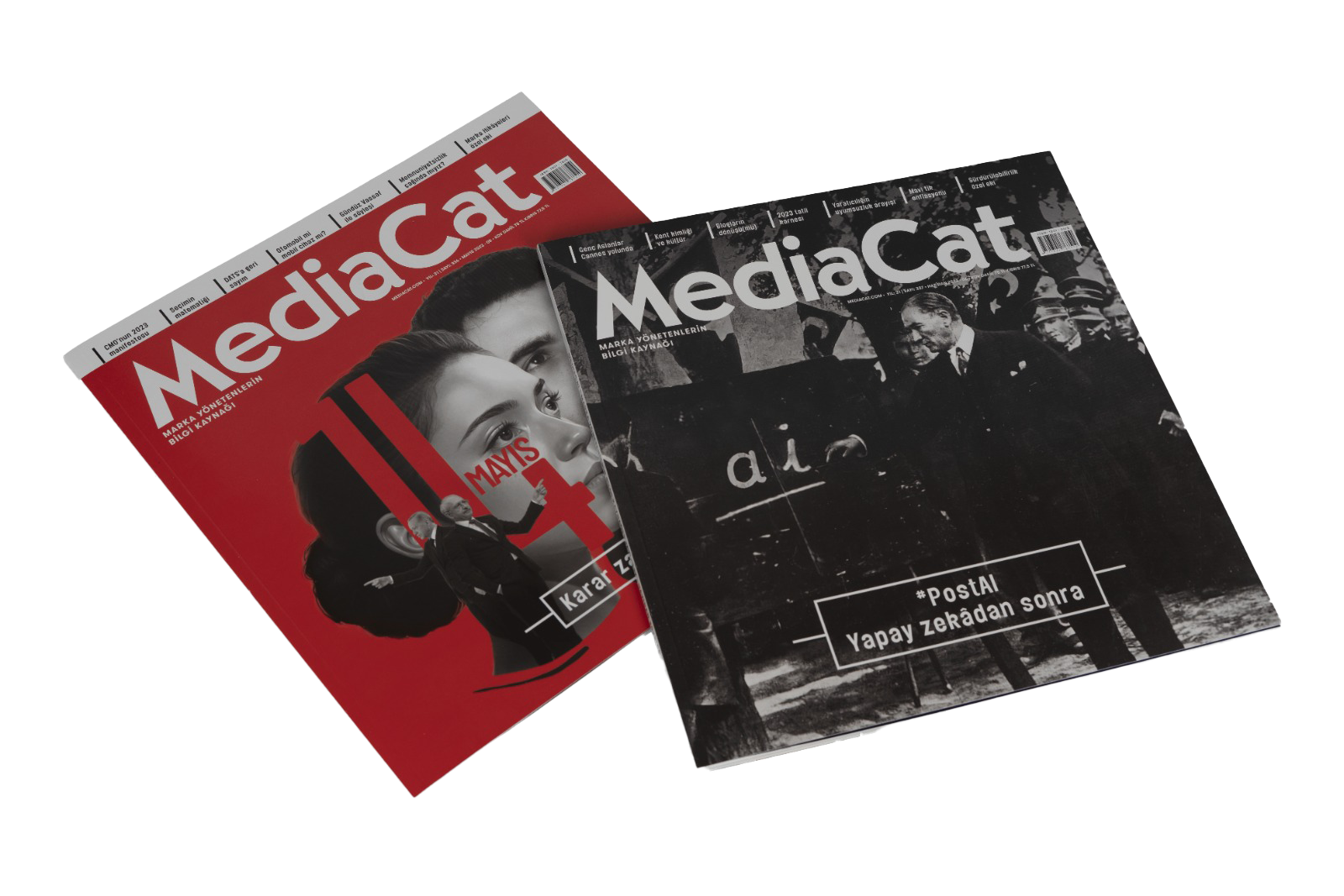
In this printing system, the printed parts are raised and firm, making the surface characteristics and elasticity of the paper important. Paper selection should be made according to the job to be printed. Matte paper is preferred for multicolored jobs in letterpress printing. Good coated papers have a smooth surface, uniform thickness, and both sides are evenly satinized, so glossiness is also important in letterpress. For less important jobs, 1st-grade paper, or even 3rd-grade paper, can be used instead of coated paper for single-color jobs.
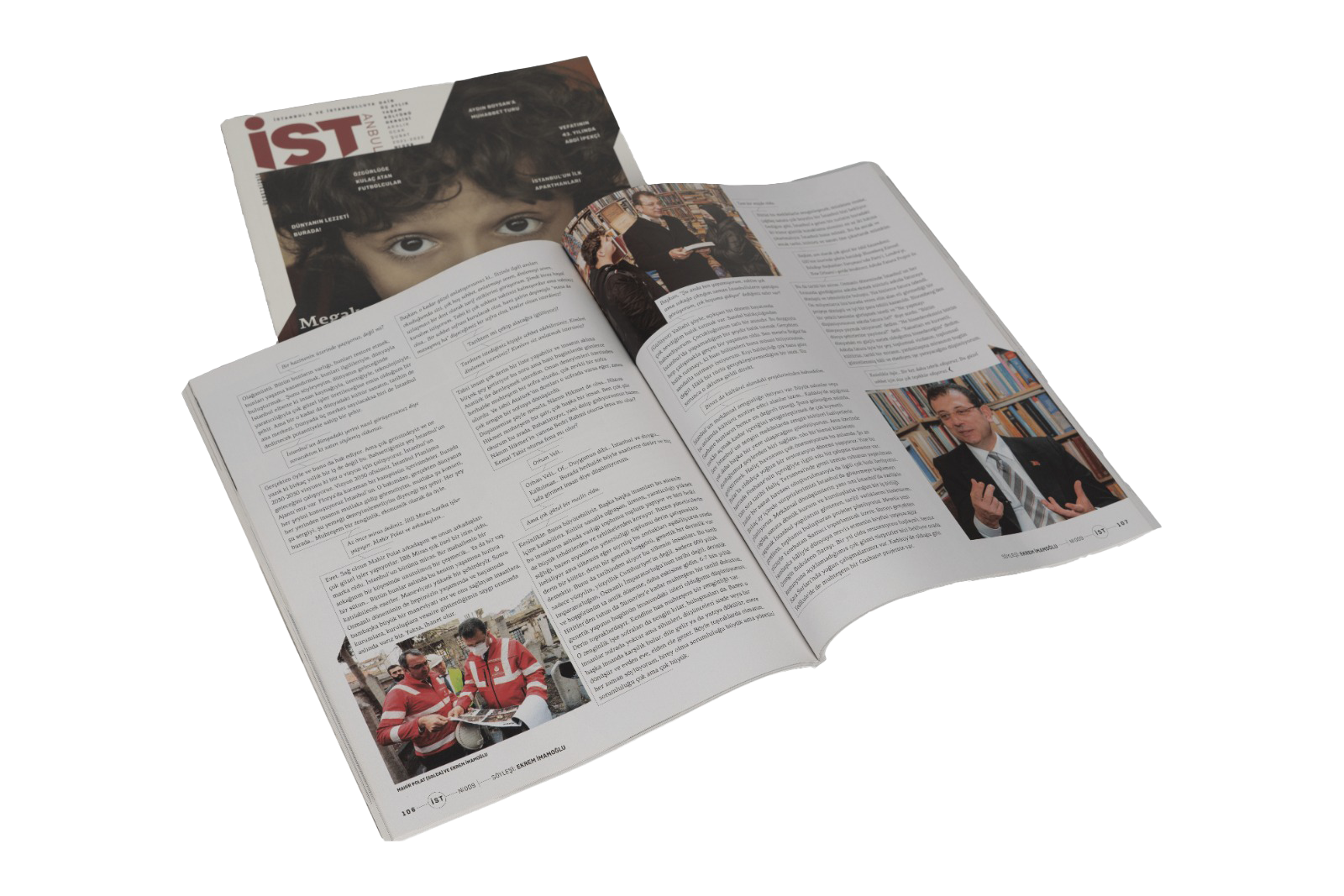
High-volume jobs and newspapers are printed using rotary offset printing machines. The papers used in these machines must be particularly strong and elastic, with the reels wound at even tension. Rotary printing is 3-4 times faster than flat offset printing, which prints on sheet paper. The paper must withstand this speed and not tear. Also, the flawless winding of the paper onto the reel is very important for machine settings. In reel printing (rotation), since the adjustment is only made from the side positions, if the reel paper passes sometimes tight and sometimes loose, it causes misalignment. For these reasons, highly sensitive electronic devices are increasingly being used in recent times.
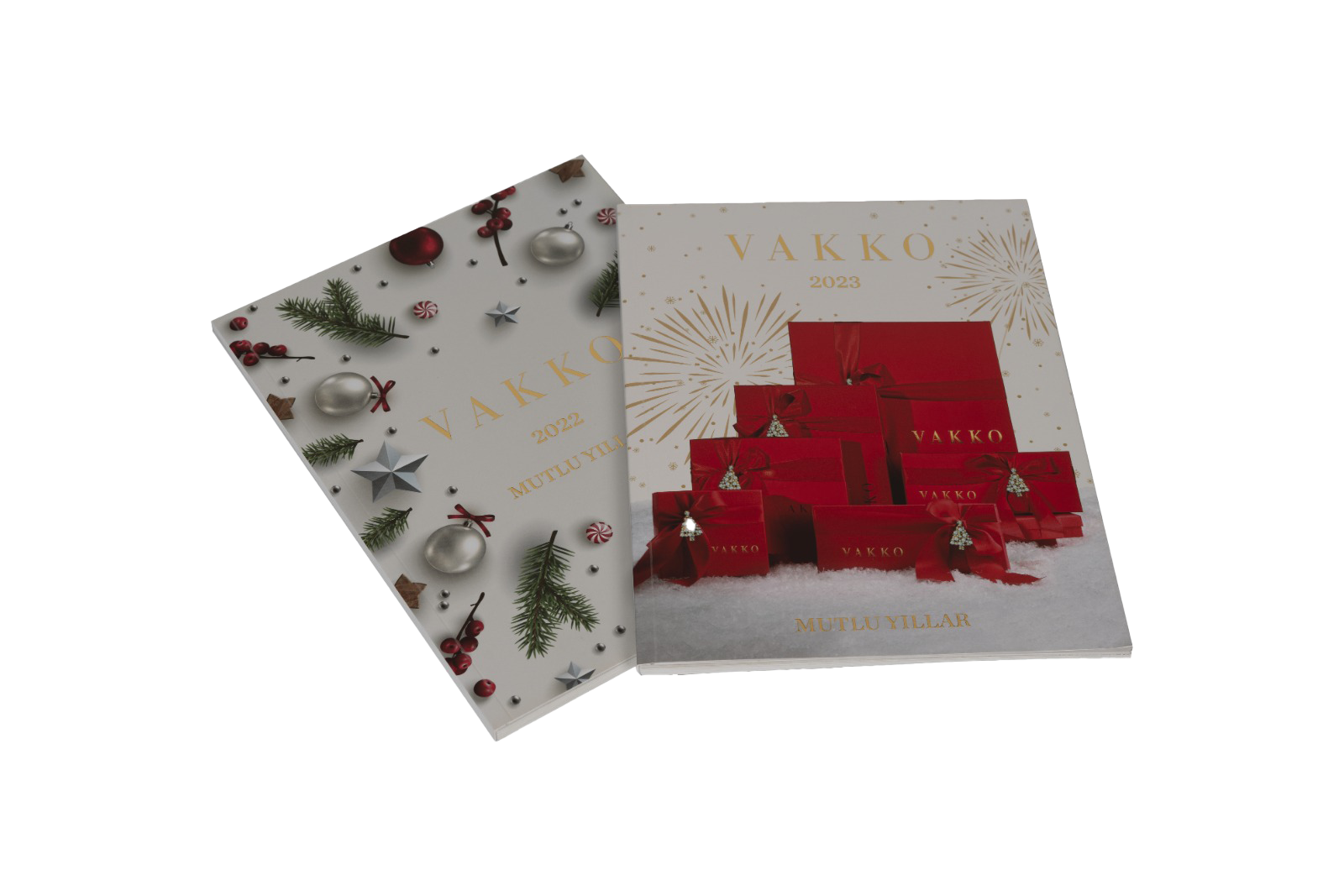
In this technique, it is possible to print on almost any type of paper. Well-glued papers yield much better results.
Binding
Binding involves folding and assembling the pages and forms of printed materials like books, magazines, brochures, and similar printed or illustrated works in their proper sequence. After forming a block, a cover is placed over them for protection. The process of fastening these together to prevent them from dispersing, and similar procedures, are called binding. The art of doing this is known as the bookbinding craft.
Quality of Offset Paper
To achieve high-quality printing and fast printing speeds, the paper is very important. The characteristics that papers used in offset printing should have are as follows:
- The surface should be smooth.
- The cut must be even.
- The paper should be properly cut in accordance with its grain direction.
- It should be receptive to printing (in terms of fibers and fillers).
- The moisture content should be normal, around 60-65%.
- It should be well-stored.
- It should not be too dusty.
Paper Standards
In rotary printing, since the papers are sold in reel form, they are ordered by the width of the reel (for example, 70 grams 1st-grade 45 cm wide reel). In machines that perform sheet printing, the paper is cut into sheets and sold in reams or packs.
Apart from these, paper of any size is available through special orders, and if necessary, custom cutting is performed on reel papers to obtain the desired size.
Paper Standards | |||||
---|---|---|---|---|---|
A0- | 841 mm x 1189 mm | B0- | 1000 mm x 1414 mm | C0- | 917 mm x 1297 mm |
A1- | 594 mm x 841 mm | B1- | 707 mm x 1000 mm | C1- | 648 mm x 917 mm |
A2- | 420 mm x 594 mm | B2- | 500 mm x 707 mm | C2- | 458 mm x 648 mm |
A3- | 297 mm x 420 mm | B3- | 350 mm x 500 mm | C3- | 324 mm x 458 mm |
A4- | 210 mm x 297 mm | B4- | 250 mm x 350 mm | C4- | 229 mm x 324 mm |
A5- | 148 mm x 210 mm | B5- | 176 mm x 250 mm | C5- | 162 mm x 229 mm |
Color Separation
- In Pantone, C’s are used for coated paper, and U’s are for uncoated paper.
- When screen printing, the film should have a maximum resolution of 70 dpi. For internally adhesive stickers, the film should be reverse emulsion.
- In offset printing, if the paper used for the film is coated, the screen ruling should be at least 80, and if uncoated paper is used, the screen ruling should be at least 60.
- For special die-cut jobs, if the film is coming out assembled, the gap between the cuts should be at least 3mm.
Lamination
- For papers under 135 grams, cellophane lamination is not applicable.
- Special papers cannot be laminated with cellophane. However, local varnish can be applied.
- In case of mounted jobs, lamination is necessary.
- For prints with dark backgrounds, to prevent cracking at the folds, cellophane or a similar coating should be applied.
- Lacquer and varnish do not prevent cracking.
Paper
- There is no weight above 170 grams for the 57×82 size.
- In hardcover, the weight should not be below 170 grams.
- Bristol and some special papers have different front and back surfaces.
- The standard size of Bristol paper is 70×100, excluding special sizes.
Frequently Asked Questions
What is a forma?
What is CTP, and what benefits does it provide?
What is CMYK?
What Should be the Format of the Images to be Used in Pre-Printing?
We want to create cardboard packaging for our upcoming product. Where should we start?
What information do I need to provide to get a price quote?
What should be considered for food packaging?